How To Implement Batch Tracking Using Manufacturing ERP
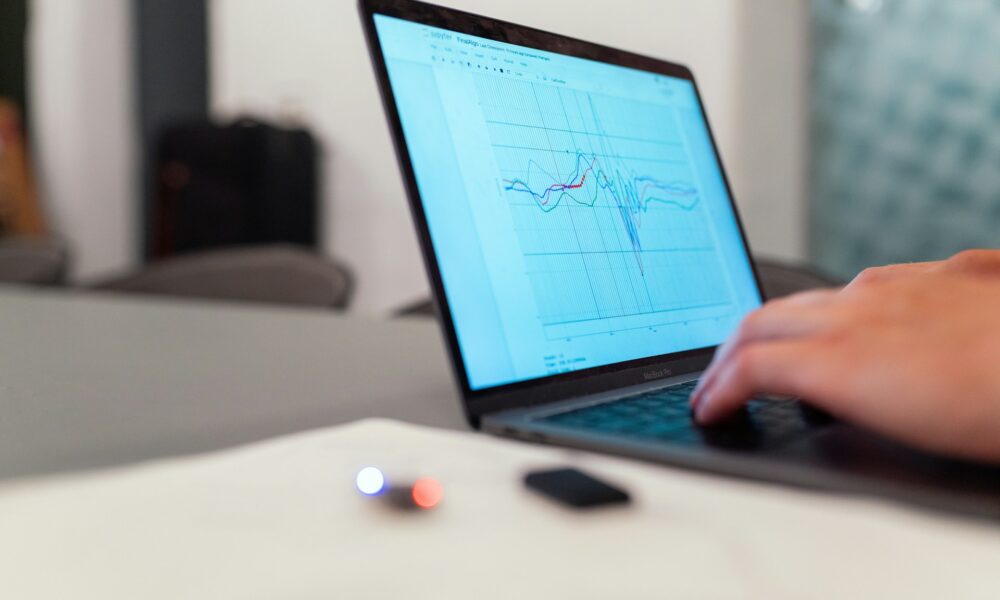
Batch tracking is a very important aspect of manufacturing management, especially for manufacturing industries dealing in huge volumes of products, or manufacturing entities that deal in perishable goods. The business is able to track the movement and status of products during the production process because of implementing batch tracking through manufacturing ERP software. This system generates live inventory, production and shipping information for businesses ensuring they uphold quality control, minimise wastage and adhere to rules and regulations. With batch tracking incorporated into manufacturing ERP, companies can accomplish streamlined operations, improve visibility, and improve traceability of the supply chain.
Assessing Operational Needs And Setting Objectives
Before a manufacturing ERP software implements batch tracking, firms will need to understand the operational needs and set clear objectives. It helps to identify the specific areas in which the batch tracking may increase the efficiency, such as raw material management or product recall process – the goals get more focused. Evaluation of existing work flows and its identification of inefficiencies enables the businesses to define the functionalities needed in an ERP system.
Measurable objectives’ definition also makes sure that the batch tracking implementation is consistent with the general business aims. Examples of objectives can be as earlier stated as reducing lead times, product recalls or order accuracy. By establishing key performance indicators (KPIs), supervision of batch tracking system effectiveness and performance monitoring is achieved with a key benchmark. Also, businesses should bring stakeholders that are crucial to the planning process so that they provide insights and create a batch tracking system that fits the operational needs of all departments.
Selecting The Right Erp System For Batch Tracking
The decision on implementation of the batch tracking is impossible without the selection of the appropriate manufacturing ERP software. All ERP systems may not be able to provide the necessary batch tracing features so that a solution must be identified that has inventory management, production scheduling and quality control modules. The targeted ERP system should have capabilities of for instance barcode scanning, lot tracking and also automatic data entry to ease batch tracking procedures.
In addition, the ERP system should also be in a position to produce detailed reports on batch status, product movement and expiry. This data helps businesses to ensure product quality, identify the defective batches, control recall of the products. Cloud-based ERP systems are especially favored in doing batch tracking because they offer real time access to data plus remote surveillance in numerous locations. Moreover, companies should also consider whether it can connect with the current software like warehouse management systems or CRM systems, to avoid rupture in information flow and enhance the visibility of operations.
Data Entry And System Integration
Data entry is an important function of introducing batch tracking in a manufacturing ERP System. Proper data input guarantees that batch recordings are correctly kept and readily available during the production cycle. Companies must create the standard data entry practices to avoid errors and ensure data continuity. This process will require one to create proper data fields for batch numbers, production dates, expiration dates and product specifications amongst other fields.
Complementary interfacing of the ERP system with other operational software increases even more the power of batch tracking. For example, the connection of the ERP system with the barcode/RFID devices enables auto data capturing, eliminating human mistake probability, and keeping the data real-time updated. Additionally, system integration allows businesses to integrate the output of batch tracking with inventory tracking software, shipping modules, and order processing modules to give the business a big picture of the product movement throughout the supply chain.
Training Employees And Managing Change
The use of batch tracking through manufacturing erp will require employees training to ensure that everyone understands the effective usage of the system. Fundamental training programs are to incorporate data entry procedures, batch tracking protocols, and report generation. Provision of continuing support and resources facilitates adaptation to the new system and overcoming possible challenges given that the system is implemented.
Implementation of batch tracking calls for equal attention to change management. The employees may be reluctant to use new technologies especially if they are used to manual tracking mechanisms. In order to redress this resistance, businesses must communicate the advantages of batch tracking, including enhanced traceability, minimized waste and accelerated recall management. Besides, the participation of employees during the planning and testing stages will make the employees feel that they own the system and that they should adapt to the new system.
Monitoring Performance And Continuous Improvement
When the batch tracking is totally deployed in the manufacturing ERP system, then organizations must continually watch performance in order to determine the effectiveness of the system. Periodic performance review can be used to detect potential bottlenecks, inconsistencies with data or some need for instruction. Observation of the non-trivial metrics (quantities), such as order accuracy, recall response time, and product expiration rates offers beneficial information about the global effects of batch tracking.
Permanent improvement is very vital to ensure effectiveness of batch tracking systems. Companies should use data emanating from the ERP system to anticipate trends, perfect production schedules, and fine tune tracking schemes. The system of periodic update of the system and the practice of regular audits also ensures that the batch tracking system is kept on par with changing operational requirements and regulations.
Conclusion
The introduction of batch tracking with the help of manufacturing ERP software is a strategic move that can highly increase the efficacy of operations, product tracking and quality control. Evaluating the operational needs, choosing the right ERP system and implementing a standardized data entry process can help businesses implement efficient batch tracking systems, which simplify production processes, and minimize the threat of errors. Training of the employees and management of change furthers a smooth transition to the new system, performance monitoring and continuous improvement helps to keep the system effective. In the final analysis, batch tracking in the manufacturing ERP optimizes operational visibility and reduces the risks associated with production efforts and sustains long-term business development.
Source: How To Implement Batch Tracking Using Manufacturing ERP